News
2022 / 04 / 09
Inconsistent Temperature and Pulling Speed During Continuous Casting Lead to Steel Breakout
One of the main operational failures encountered in continuous casting is “breakout”. When the strand shell breaks, the still molten molten steel in the mould assembly shell overflows, blocking the copper mould tube machine and requiring costly downtime. In order to pull out the breakout billet shell, it is necessary to prolong the downtime caused by the breakout, because it may block the guide roll or foot roll, and it is necessary to use gas cutting to clear the blockage and pull out the billet shell. When the temperature of the breakout shell decreases, it needs to be cut into small pieces and taken out of the machine with a straightening machine. The straightening machine is designed to gradually straighten the cold billet shell in the stable stage, and the upper roll can provide sufficient Raise gravity to make a curved strand that isn’t too long. Therefore, breakout has a major impact on the effectiveness of the caster – affecting both productivity and production costs.
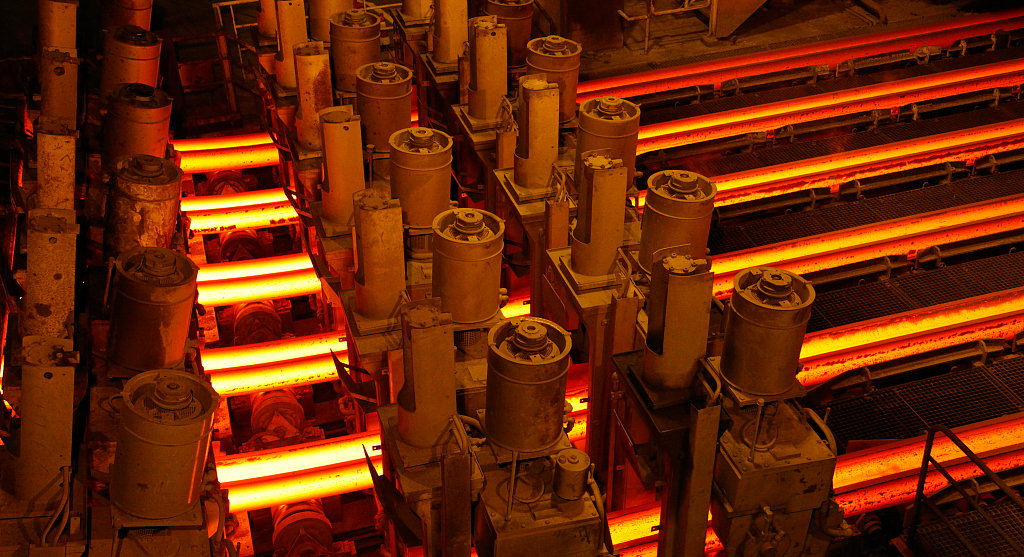
Inconsistent temperature and pulling speed – the higher the superheat of the molten steel, the thinner the copper mould tube shell thickness. The shell expands due to the static pressure exerted by the molten steel in the mold. When the strength of the billet shell is not enough, breakout is easy to occur. Inconsistent and uneven temperatures have a great impact on the generation of breakout. When the pulling speed increases, breakout is more likely to occur because the copper mould tube is not lubricated enough. From the meniscus to the mould assembly shell/copper mould tube wall, the copper mould tube flux has poor fluidity, and increasing the pulling speed will lead to the total heat release. reduce. Breakout is often caused by pulling rates that are too high, when the billet shell does not have enough time to solidify to the required thickness, or the metal is too hot, which means that final solidification occurs just below the straightening rolls, due to the stress applied during straightening, the billet Shell torn. When the carbon content in the steel is constant, the temperature is high and the pulling speed is fast, and the steel breakout is easy to occur. Any change in the vibration setting will cause breakout to occur, as reducing vibration marks by increasing the vibration frequency increases the mold assembly velocity and thus the friction at the interface.
Contact Us
Address
High-tech Industrial Development Zone, Zhengzhou City, Henan Province, China.
jean@ji-steel.com
Phone
+86 188 3804 2177
Products
- Continuous Casting
- ● Copper Mould Tube
- ● Mould Assembly
- Steel Melting
- ● Graphite Electrode
- Refractory Material
- ● Nozzle Bricks
- ● Magnesia Carbon Brick
- ● High Alumina Brick
Contact
- jean@ji-steel.com
- +86 371 6781 0168
- +86 188 3804 2177
- +86 188 3804 2177
- www.ji-steel.com
- High-tech Industrial Development Zone, Zhengzhou City, Henan Province, China.
Quick Links
© Copyright 2022 JI Steel. All right reserved.