News
2022 / 06 / 13
Refractory for ferrosilicon furnace

Ferrosilicon furnace is an industrial electric furnace with large power consumption, and it is a kind of submerged arc furnace. Ferrosilicon furnace has furnace shell, furnace cover, furnace lining, short net, water cooling system, smoke exhaust system, dust removal system, electrode shell, electrode pressing and lifting system, loading and unloading system, controller, burn-through device, hydraulic system, transformer And various electrical equipment and other components, the use of refractory materials is also quite strict.
The ferrosilicon furnace mainly produces ferrosilicon, ferromanganese, ferrochromium, ferrotungsten, and silicon-manganese alloy. The production form is continuous feeding and intermittent tapping of iron slag, which is an industrial electric furnace for continuous operation.
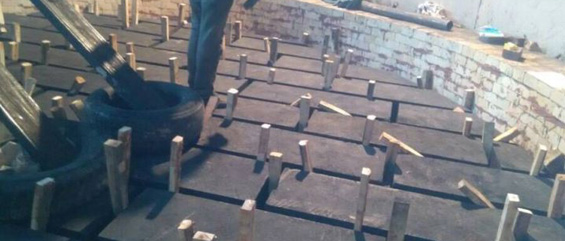
The ferrosilicon furnace is a type of high energy consumption furnace, which reduces energy consumption and increases output, so that the life of the furnace can be used for a long time. Only in this way can the production cost of the enterprise be reduced and the discharge of waste residue pollutants be reduced. The following introduces the different reaction temperatures of the ferrosilicon furnace, and the use of refractory materials of different materials is for reference only.
New material preheating zone: the uppermost layer is about 500mm, the high temperature airflow with the temperature of 500℃-1000℃, the electrode conduction heat, the combustion of the surface charge and the charge distribution current resistance heat, the temperature of this part is different, and the clay brick is used as the lining.
Preheating zone: After the water evaporates, the charge will gradually go down and undergo a preliminary change in the preheating zone. Silica crystal transformation, volume expansion, and then cracks or bursts occur. The temperature in this section is about 1300°C. Built with high alumina bricks.
Sintering zone: It is the crucible shell, the temperature is 1500℃-1700℃, liquid silicon and iron are formed and drop into the molten pool. The sintering and air permeability of the charge are poor. The block material should be broken, the gas ventilation should be restored, and the resistance should be increased. The temperature in this area is high. Aggressive. It is built with semi-graphitic carbon–silicon carbide bricks.
Reduction zone: a large number of intense chemical reactions of materials, the temperature of the crucible zone is 1750℃-2000℃, the lower part is connected to the arc chamber, mainly for the decomposition of SIC, the generation of ferrosilicon, the reaction of liquid Si2O with C, Si, etc. The high temperature area must be built with semi-graphite fired carbon bricks.
Arc area: In the cavity area at the bottom of the electrode, the temperature is above 2000°C. The temperature in this area is the highest temperature area in the entire furnace and the source of the most temperature distribution in the entire furnace body. Therefore, when the electrode is inserted shallowly, the high temperature area moves up, and the furnace bottom temperature Low slag removal is less, forming a false bottom, causing the tap hole to move up, and a certain false bottom has certain benefits for furnace protection. Generally speaking, the insertion depth of the electrode has a lot to do with the diameter of the electrode. Generally, the insertion depth should be kept at 400mm-500mm from the bottom of the furnace. This part has a higher temperature and is built with semi-graphite fired carbon bricks.
Phosphate concrete or clay bricks are used for permanent layers. The furnace door can be cast with corundum castables or pre-laid with silicon carbide bricks.
Contact Us
Address
High-tech Industrial Development Zone, Zhengzhou City, Henan Province, China.
jean@ji-steel.com
Phone
+86 188 3804 2177
Products
- Continuous Casting
- ● Copper Mould Tube
- ● Mould Assembly
- Steel Melting
- ● Graphite Electrode
- Refractory Material
- ● Nozzle Bricks
- ● Magnesia Carbon Brick
- ● High Alumina Brick
Contact
- jean@ji-steel.com
- +86 371 6781 0168
- +86 188 3804 2177
- +86 188 3804 2177
- www.ji-steel.com
- High-tech Industrial Development Zone, Zhengzhou City, Henan Province, China.
Quick Links
© Copyright 2022 JI Steel. All right reserved.