News
2025/ 02 / 18
Supporting Equipment for Electric Arc Furnace Steelmaking: Building an Efficient and Green Steel Production System
Electric arc furnace (EAF) steelmaking, as a crucial process in modern steel production, is increasingly prominent in the steel industry due to its advantages of flexibility, efficiency, and environmental friendliness. A comprehensive set of supporting equipment for EAF steelmaking is key to achieving efficient, stable, and green production. This article provides a detailed introduction to the supporting equipment required for EAF steelmaking, covering the furnace body, raw material processing, secondary refining, and continuous casting and rolling.
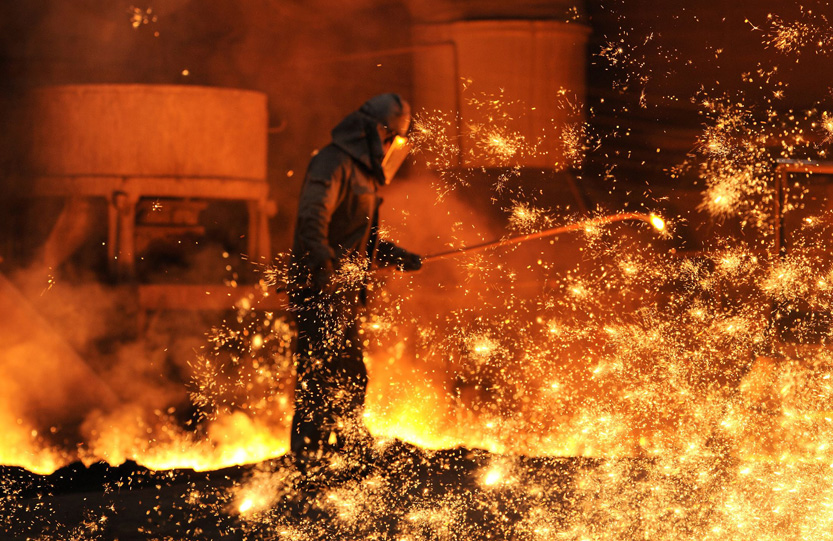
I. Furnace Body Equipment: The Core of Energy Conversion
The furnace body is the core equipment of EAF steelmaking, responsible for converting electrical energy into thermal energy to melt the charge and refine the molten steel. Based on the method of energy input, EAFs are mainly divided into two categories: arc furnaces and induction furnaces.
Arc Furnace: Utilizes high-temperature arcs generated between electrodes and the charge for heating. It features fast heating, high furnace temperatures, and strong adaptability, making it the most widely used type of EAF. The main components of an arc furnace include:
Furnace Shell: Composed of the furnace shell, lining, and roof, it contains the charge and molten steel while withstanding high temperatures and chemical erosion.
Electrode System: Includes electrodes, electrode holders, and electrode lifting mechanisms, which deliver electrical energy into the furnace and form arcs.
Transformer: Supplies the required electrical energy to the arc furnace and regulates voltage and current.
Cooling System: Cools the furnace shell, electrodes, and other components to prevent overheating and damage.
Induction Furnace: Uses electromagnetic induction to generate eddy currents within the charge for heating. It offers uniform heating, minimal element loss, and low environmental pollution, making it suitable for smelting special steels and alloys. The main components of an induction furnace include:
Induction Coil: Carries alternating current to generate an alternating magnetic field, inducing eddy currents in the charge.
Furnace Body: Made of refractory materials, it contains the charge and molten steel.
Power Supply System: Provides the necessary electrical energy to the induction coil.
II. Raw Material Processing Equipment: Ensuring Stable Production
EAF steelmaking has strict requirements for the size, composition, and dryness of raw materials. Therefore, a complete set of raw material processing equipment is essential to ensure production stability and product quality.
Scrap Preprocessing Equipment: Includes scrap crushers, balers, and shears, which process scrap steel into the required sizes and shapes.
Alloy Addition Equipment: Includes storage bins, weighing devices, and conveying equipment, which accurately add various ferroalloys to adjust the molten steel composition.
Auxiliary Material Addition Equipment: Includes equipment for adding slag-forming materials such as limestone and dolomite to control slag composition and properties.
III. Secondary Refining Equipment: Enhancing Molten Steel Quality
Secondary refining is a critical component of the EAF steelmaking process, further removing impurities, adjusting composition and temperature, and improving molten steel quality.
LF Furnace: Uses arc heating and argon stirring for desulfurization, deoxidation, alloying, and temperature adjustment of molten steel.
VD Furnace: Employs vacuum degassing technology to remove hydrogen, nitrogen, and other gases from molten steel.
RH Furnace: Utilizes vacuum circulation degassing technology, offering higher degassing efficiency and lower processing costs.
IV. Continuous Casting and Rolling Equipment: Embodiment of Efficient Production
Continuous casting and rolling is an advanced process that directly casts molten steel into billets and rolls them into finished products. It offers high production efficiency, low energy consumption, and high yield rates.
Continuous Caster: Continuously casts molten steel into billets of specific cross-sectional shapes. Key components include the ladle turret, tundish, mold, and withdrawal machine.
Rolling Mill: Rolls the continuously cast billets into various steel products. Key components include the reheating furnace, roughing mill, finishing mill, and cooling equipment.
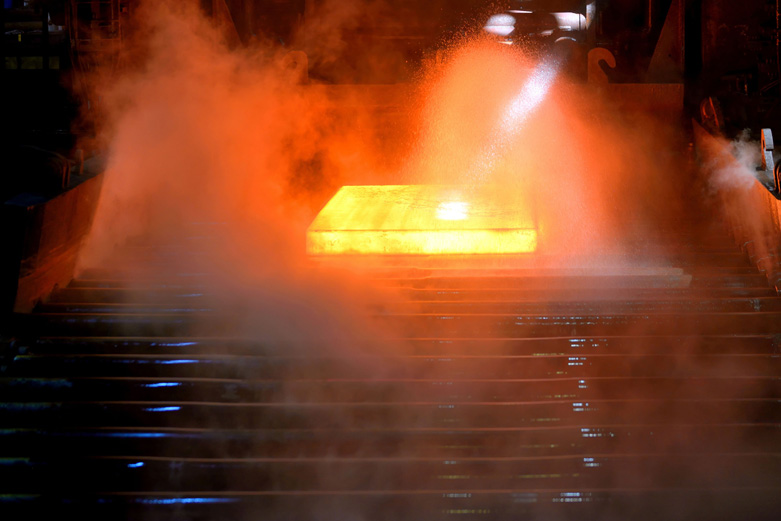
V. Other Auxiliary Equipment:
Dust Collection System: Collects and treats dust generated during EAF steelmaking to reduce environmental pollution.
Water Treatment System: Treats wastewater generated during EAF steelmaking for recycling.
Automated Control System: Enables automated control of the EAF steelmaking process, improving production efficiency and product quality.
The supporting equipment for EAF steelmaking is a complex and extensive system, with interconnected and interdependent components. With the continuous advancement of science and technology, EAF steelmaking equipment is also evolving, moving toward greater efficiency, energy savings, and environmental friendliness. In the future, EAF steelmaking equipment will become more intelligent and automated, providing robust support for the sustainable development of the steel industry.
Contact Us
Address
High-tech Industrial Development Zone, Zhengzhou City, Henan Province, China.
jean@ji-steel.com
Phone
+86 188 3804 2177
Products
- Continuous Casting
- ● Copper Mould Tube
- ● Mould Assembly
- Steel Melting
- ● Graphite Electrode
- Refractory Material
- ● Nozzle Bricks
- ● Magnesia Carbon Brick
- ● High Alumina Brick
Contact
- jean@ji-steel.com
- +86 371 6781 0168
- +86 188 3804 2177
- +86 188 3804 2177
- www.ji-steel.com
- High-tech Industrial Development Zone, Zhengzhou City, Henan Province, China.
Quick Links
© Copyright 2022 JI Steel. All right reserved.