News
2025/ 03 / 04
Precautions for the use of copper mould tubes in the continuous casting process of steelmaking
Introduction
The crystallizer is one of the core equipment in the continuous casting process, and the copper mould tube is a key component of the crystallizer. Its performance and use status directly affect the quality and production efficiency of the continuous casting billet. Copper tubes work under high temperature, high pressure and strong cooling conditions, and are easily affected by thermal stress, wear and chemical corrosion. Therefore, the reasonable use and maintenance of the copper mould tube is crucial to ensure the stability of the continuous casting process and product quality. This article will discuss the precautions for the use of copper mould tubes in the continuous casting process of steelmaking from the aspects of copper tube selection, installation, use and maintenance.
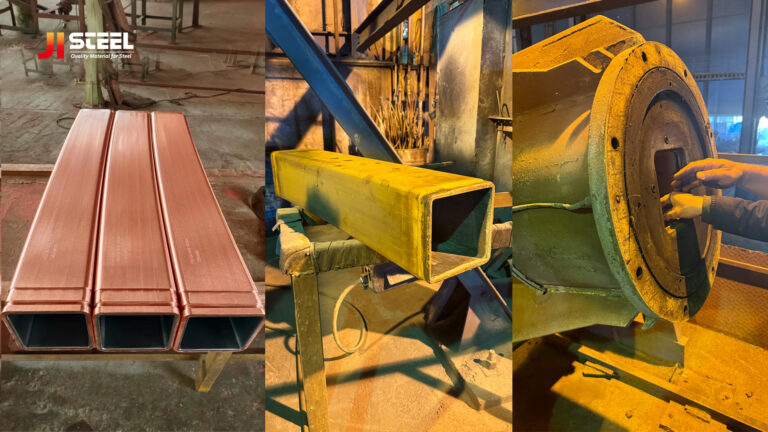
1. Selection of copper mould tubes
Material selection
The material of the copper mould tube should have high thermal conductivity, good wear resistance and thermal fatigue resistance. Commonly used materials include chromium zirconium copper (CuCrZr) and silver copper (CuAg). Chromium zirconium copper is widely used due to its excellent comprehensive properties (high hardness, good thermal conductivity and thermal fatigue resistance).
Dimensional accuracy
The inner and outer diameters, wall thickness and taper of the copper tube must meet the design requirements to ensure that the molten steel is evenly cooled and solidified in the crystallizer. Dimensional deviations can cause defects such as cracks and depressions on the surface of the ingot.
Surface quality
The inner surface of the copper tube should be smooth and free of defects to reduce scratches and cracks on the surface of the ingot. The outer surface should have a good coating (such as nickel-cobalt coating) to improve wear resistance and corrosion resistance.
2. Installation of copper mould tube
Inspection before installation
Check whether there are cracks, scratches or corrosion marks on the surface of the copper tube.
Measure the dimensional accuracy of the copper tube to ensure that it meets the process requirements.
Check whether the cooling water channel is unobstructed to avoid local overheating due to blockage.
Precautions during installation
The copper tube should fit tightly with the shell of the crystallizer to avoid uneven cooling due to excessive gaps.
Special tools should be used during installation to avoid mechanical damage to the surface of the copper tube.
Ensure that the taper direction of the copper tube is consistent with the design to ensure smooth solidification and shrinkage of the ingot.
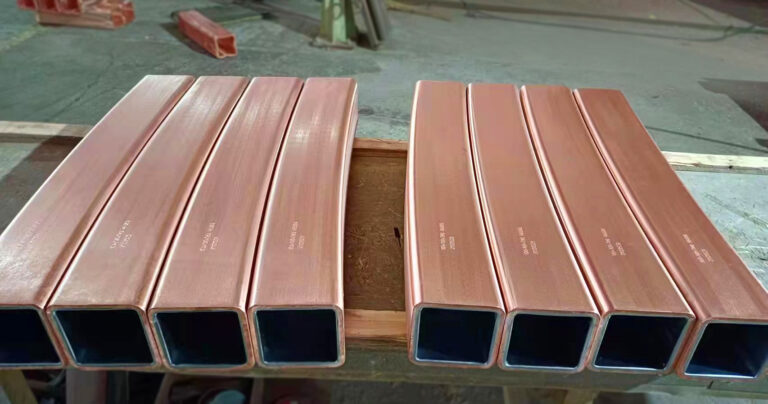
3. Use of copper mould tube
Cooling water management
The flow, pressure and temperature of cooling water should be strictly controlled to ensure uniform surface temperature of copper tube and avoid local overheating or overcooling.
The quality of cooling water should be tested regularly to prevent scale or impurities from blocking cooling channel.
Drawing speed control
Excessive drawing speed will lead to excessive surface temperature of copper tube, accelerate wear and thermal fatigue of copper tube; too slow speed may lead to deterioration of surface quality of ingot. The drawing speed should be reasonably adjusted according to steel type and ingot size.
Use of protective slag
The thickness and distribution of protective slag should be uniform to reduce friction between copper tube and ingot, prevent direct contact between molten steel and copper tube, and reduce wear and thermal stress of copper tube.
4. Maintenance of copper mould tube
Regular inspection
Regularly check the inner and outer surfaces of copper tube to find defects such as cracks, wear or corrosion in time.
Use ultrasonic detection and other means to evaluate the wall thickness change of copper tube to ensure that it is within the safe range.
Surface repair
For minor surface damage, grinding or polishing can be used to repair; for severe wear or cracks, the copper tube should be replaced in time.
Regularly re-plating the outer surface of the copper tube to restore its wear resistance and corrosion resistance.
Replacement cycle
According to the use and production records of the copper tube, a reasonable replacement cycle should be established. Normally, the service life of the copper tube is thousands of furnaces, but the specific cycle needs to be adjusted according to the actual working conditions.
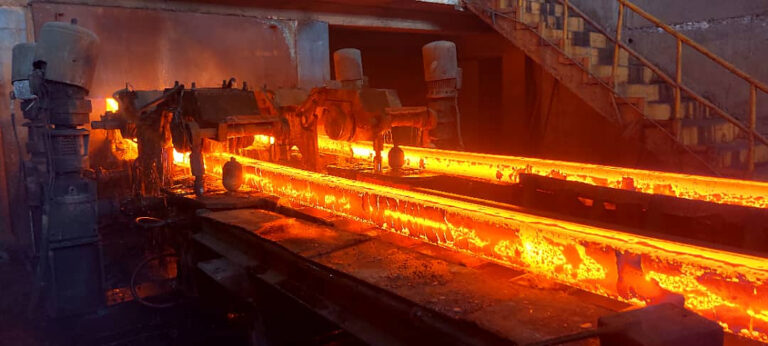
5. Common problems and solutions
Cracks on the surface of the copper tube
Cause: Excessive thermal stress or uneven cooling.
Solution: Optimize cooling water parameters to ensure uniform cooling; regularly check the surface state of the copper tube.
Surface defects of the ingot
Cause: Rough inner surface of the copper tube or dimensional deviation.
Solution: Replace or repair the copper tube to ensure its surface quality and dimensional accuracy.
Copper tube wears too fast
Reason: Too fast casting speed or improper use of protective slag.
Solution: Adjust casting speed and optimize the amount and distribution of protective slag.
Conclusion
The copper mould tube plays a vital role in the steelmaking continuous casting process, and its use status directly affects the quality of the ingot and production efficiency. Through reasonable selection, standardized installation, scientific use and regular maintenance, the service life of the copper tube can be effectively extended, the production cost can be reduced, and the stability of the continuous casting process and product quality can be improved. In actual production, targeted management and maintenance strategies should be formulated in combination with specific working conditions to ensure that thecopper mould tube is always in the best working condition.
JISTEEL boasts a comprehensive product portfolio encompassing not only copper mould tube but also a myriad of related components essential for crystallization processes. The company offers a one-stop solution for customers seeking complete crystallizer assemblies tailored to their specific requirements.
Contact Us
Address
High-tech Industrial Development Zone, Zhengzhou City, Henan Province, China.
jean@ji-steel.com
Phone
+86 188 3804 2177
Products
- Continuous Casting
- ● Copper Mould Tube
- ● Mould Assembly
- Steel Melting
- ● Graphite Electrode
- Refractory Material
- ● Nozzle Bricks
- ● Magnesia Carbon Brick
- ● High Alumina Brick
Contact
- jean@ji-steel.com
- +86 371 6781 0168
- +86 188 3804 2177
- +86 188 3804 2177
- www.ji-steel.com
- High-tech Industrial Development Zone, Zhengzhou City, Henan Province, China.
Quick Links
© Copyright 2022 JI Steel. All right reserved.